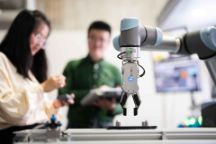
Factory of the Future
Where people and technologies come together to make manufacturing smarter, safer, greener and more sustainable.
Established in 2015, Swinburne’s Factory of the Future is a digital manufacturing technology centre, co-creating innovative solutions with industry – for industry. We’re the first dedicated state-of-the-art Industry 4.0 facility in Australia.
We empower manufacturing small-to-medium enterprises (SMEs) to overcome digital technology adoption challenges.
The Factory of the Future provides access to a dedicated digital technology prototyping facility, workforce training and a diverse multi-disciplinary team of seasoned academic and industry professionals to help you negotiate your challenges and exploit smart manufacturing methodologies and digital technologies.
We’re also a gateway for Bachelor, Master and HDR graduate students to access cutting-edge training and education opportunities.

Meet your Industry 4.0/5.0 partners
Digitalisation and technology adoption is a transformative journey, requiring careful, considered planning.
At the Factory of the Future, we understand Industry 4.0/5.0’s benefits, as well as the need to respect the interplay between people, processes and technology.
We can help you to adopt digital technology in your manufacturing processes through:
helping you to understand digital technologies
co-developing new products or methods of manufacturing
finding ways for you to be more productive or create new value-added business models.
Why Factory of the Future?
Wealth of experience
We have serviced diverse sectors, including advanced manufacturing, energy, defence, food and beverages, logistics and supply chain, agriculture, transport, textiles, medtech, digital health, and construction.
Broad expertise
Our expertise spans analysis and execution of operational improvements, optimisations in manufacturing, research translation, end-to-end digital prototyping and innovation, and much more.
World-class research
Discover cutting-edge research in industrial IoT, digital twins, mixed reality, net zero, robotics, automation and control, AI and machine learning, additive manufacturing, and allied emerging digital technologies.
Tailored support
Through our semi-consulting offering, we advise on digital technology adoption that best suits the needs of your business. We also help create your own internal Industry 4.0/5.0 champions.
Blueprint for modern innovation
Working in collaboration with Digital Innovation Lab, industry partners, Design Factory Melbourne, Swinburne's PAVE, schools, institutes and centres, we set new standards in university and industry engagement.






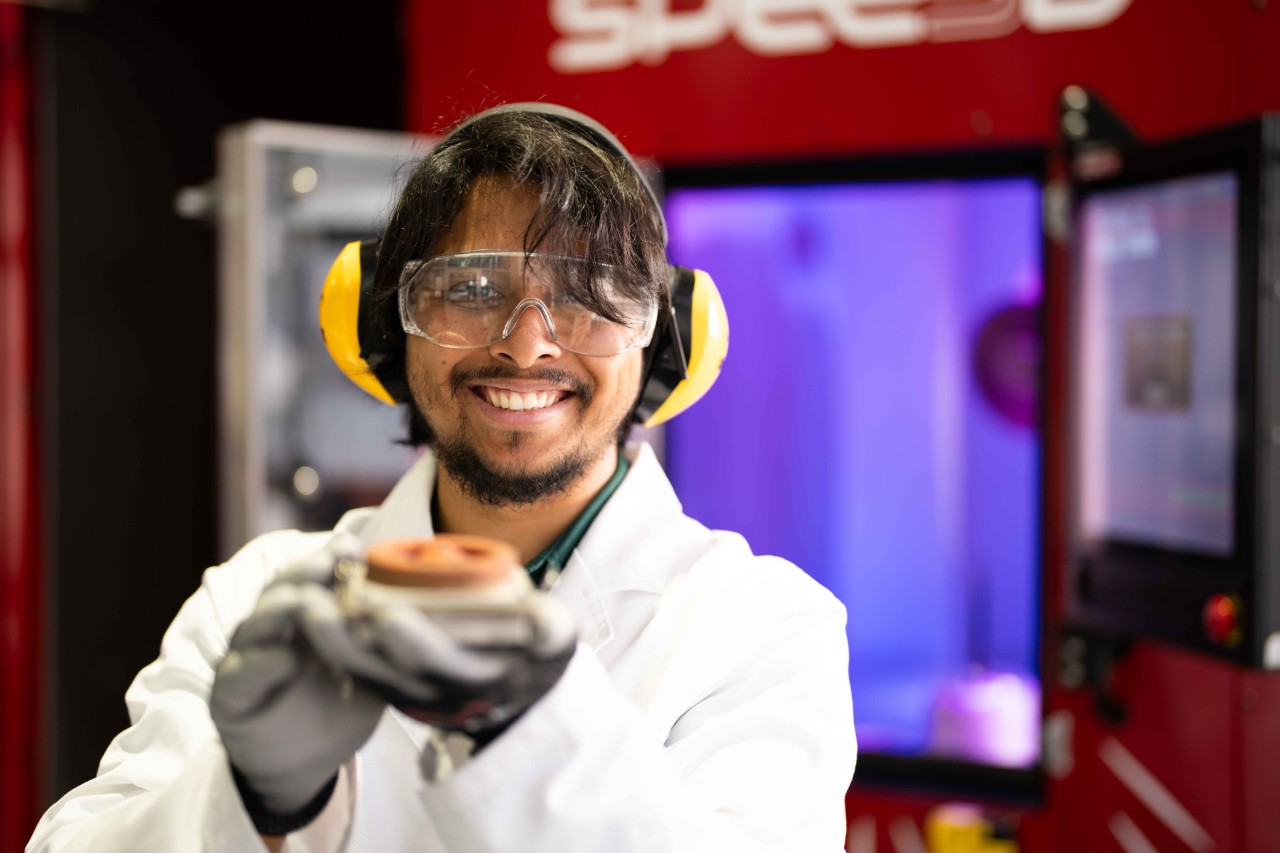




-
Co-Robot in action
-
Business Readiness Lego Serious Play Session
-
Student internship projects
-
Additive Manufacturing (Markforge)
-
Hydrogen-Powered Drone – AIR Hub
-
Hydrogen-Powered Drone – AIR Hub
-
Additive Manufacturing (Spee3D)
-
Cyber Physical Factory
-
Cyber Physical Factory in action
-
Virtual Reality – Digital Technologies
-
Augmented Reality – Digital Technologies
Capabilities and services
At the Factory of the Future’s Technology Centre, you’ll access a range of technologies demonstrating and exploring Industry 4.0/5.0.
We offer a unique, nation-first university-based business. We provide consulting for Industry 4.0/5.0 digital readiness, as well as a transformation program.
Discover design to manufacture design and engineering, including world-class additive manufacturing processes, at the Factory of the Future.
Build your business by leveraging our world-renowned expertise in AI and machine learning, developing smart, agile and innovative industry solutions.
Work with us to develop robust, industry-ready software solutions that help to bolster your digital manufacturing processes.
We offer extensive capabilities in key areas of digital manufacturing, additive manufacturing, net zero, digital twins, and industrial Internet of Things.
Our program enables business model innovation through outcome-based advanced services and Industry 4.0/5.0, in collaboration with Advanced Services Group, UK.
Welcome to the Factory of the Future
Located on the ground floor of Swinburne’s A$100 million Advanced Manufacturing and Design Centre (AMDC Building), the Factory of the Future features state-of-the-art manufacturing tools and technologies.
Our ground-breaking facility is made up of a cluster of specialist equipment, used to:
showcase the use and potential of technology in industry
support research and innovation in digital manufacturing and industry collaboration projects.
Working with us
Our team would be delighted to hear from you. Let’s talk about working together to:
explore the technology set demonstrating Industry 4.0/5.0
better understand the digital readiness of your business
identify how Industry 4.0/5.0 can help with your business model innovation, such as through servitisation
learn how artificial intelligence, machine learning or software-engineered, industry-ready solutions can impact on your business
set up internships and training opportunities
undertake applied R&D
address other requirements specific to your business.
Contact the Factory of the Future via factoryofthefuture@swinburne.edu.au – or feel free to reach out to a member of our team.
Staff name | Role | Contact details |
---|---|---|
Professor Prem Prakash Jayaraman | Director | |
Shuo Wang | Senior Technical Officer | shuowang@swinburne.edu.au |
Dr Abhik Banerjee | Associate Director, Digital Innovation Lab | abanerjee@swinburne.edu.au |
Dr Abdur Forkan | Senior Research Fellow, AI and ML, Digital Innovation Lab | fforkan@swinburne.edu.au |
Vikram Sachdeva | Head, Manufacturing Excellence | |
Vince Lorefice | Industry 4.0 Transformation Consultant | |
Dr Sharad Menon | Director, Industry Engagement and Business Development, Innovation & Enterprise | sharadmenon@swinburne.edu.au |
Keep exploring
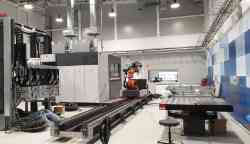
Swinburne-CSIRO National Industry 4.0 Testlab
The Swinburne-CSIRO National Industry 4.0 Testlab conducts industrial scale multilayer 3D printing for near net composite manufacturing and solutions for automotive and aerospace parts, processes and systems.
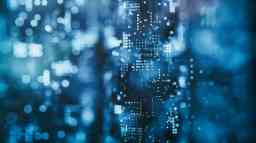
Digital Innovation Lab
Swinburne’s Digital Innovation Lab enables research translation and innovation by bringing together multi-disciplinary research capabilities across the university, provides software engineering competency and offers a space for co-creation, co-design and experimentation.
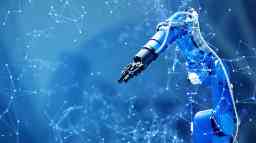
Manufacturing Futures Research Platform
The Manufacturing Futures Research Platform integrates advanced manufacturing in the global value chain to secure Australia’s industrial future.
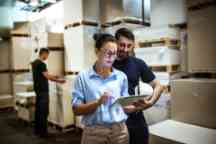
Industrial Digital Transformation Hub
Improve your productivity and quality, innovate your business model and create new revenue streams by connecting into global supply chains and enhancing your global competitiveness.
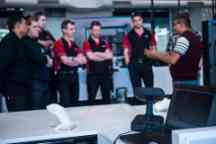
Our partners
We work with industry partners to solve key challenges through integration of innovative design platforms, advanced manufacturing technologies, digitalization and information systems. View our key strategic and industry partnership.
-
Swinburne-CSIRO National Industry 4.0 Testlab
The Swinburne-CSIRO National Industry 4.0 Testlab conducts industrial scale multilayer 3D printing for near net composite manufacturing and solutions for automotive and aerospace parts, processes and systems.
-
Digital Innovation Lab
Swinburne’s Digital Innovation Lab enables research translation and innovation by bringing together multi-disciplinary research capabilities across the university, provides software engineering competency and offers a space for co-creation, co-design and experimentation.
-
Manufacturing Futures Research Platform
The Manufacturing Futures Research Platform integrates advanced manufacturing in the global value chain to secure Australia’s industrial future.
-
Industrial Digital Transformation Hub
Improve your productivity and quality, innovate your business model and create new revenue streams by connecting into global supply chains and enhancing your global competitiveness.
-
Our partners
We work with industry partners to solve key challenges through integration of innovative design platforms, advanced manufacturing technologies, digitalization and information systems. View our key strategic and industry partnership.
Explore our news

- Technology
- Science
- Engineering
Creating safer, more accessible processed foods with innovative AI-powered digital twin system
A new initiative is applying AI to food processing, using digital twins to ensuring texture modified foods such as purees and soups are safe for vulnerable Australians.

- Technology
Swinburne enters the metaverse with Factory of Future digital twin
Swinburne University of Technology’s state-of-the-art Factory of the Future will be the latest space to enter the metaverse through a new partnership with tech leader CWX Technologies.

- Engineering
- Aviation
Pioneering Markforged 3D printer makes Australian debut
Swinburne’s Factory of the Future will play host to the Markforged FX20 printer to support the creation of lighter, stronger and more resilient end-use parts.
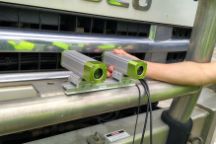
- Technology
- Engineering
5G garbage trucks driving the future of smart cities
A pioneering Swinburne partnership with Brimbank City Council will help identify roadside issues and slash maintenance costs, supported by the Federal Government.
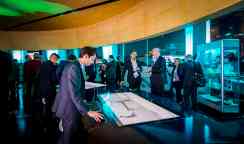
- University
Swinburne-Siemens partnership is building the workforce of the future
Swinburne’s partnership with Siemens is enabling our students to work with industry and researchers, developing and co-creating new technologies and practices.

- University
Festo, TUM Asia and Swinburne focus on the future of Industry 4.0
Festo, the Technical University of Munich in Asia (TUM Asia) and Swinburne have signed a Memorandum of Understanding.
-
- Technology
- Science
- Engineering
Creating safer, more accessible processed foods with innovative AI-powered digital twin system
A new initiative is applying AI to food processing, using digital twins to ensuring texture modified foods such as purees and soups are safe for vulnerable Australians.
Thursday 23 January 2025 -
- Technology
Swinburne enters the metaverse with Factory of Future digital twin
Swinburne University of Technology’s state-of-the-art Factory of the Future will be the latest space to enter the metaverse through a new partnership with tech leader CWX Technologies.
Wednesday 08 March 2023 -
- Engineering
- Aviation
Pioneering Markforged 3D printer makes Australian debut
Swinburne’s Factory of the Future will play host to the Markforged FX20 printer to support the creation of lighter, stronger and more resilient end-use parts.
Friday 28 October 2022 -
- Technology
- Engineering
5G garbage trucks driving the future of smart cities
A pioneering Swinburne partnership with Brimbank City Council will help identify roadside issues and slash maintenance costs, supported by the Federal Government.
Friday 04 February 2022 -
- University
Swinburne-Siemens partnership is building the workforce of the future
Swinburne’s partnership with Siemens is enabling our students to work with industry and researchers, developing and co-creating new technologies and practices.
Monday 24 August 2020 -
- University
Festo, TUM Asia and Swinburne focus on the future of Industry 4.0
Festo, the Technical University of Munich in Asia (TUM Asia) and Swinburne have signed a Memorandum of Understanding.
Wednesday 22 July 2020
Contact the Factory of the Future
Contact us to enquire about solutions for your business, our projects and our initiatives. To engage with us across our Industry 4.0 capabilities, please contact Prem Prakash Jayaraman, Director, Factory of the Future on +61 3 9214 8587 or via pjayaraman@swinburne.edu.au to start a conversation.