What is low-carbon steel?

In summary
- Swinburne Professor of Engineering, Geoff Brooks provides a low-carbon steel explainer.
The Australian Government’s new energy roadmap includes a plan to produce ‘low carbon steel’. Is this just a buzz word or some pipe dream?
Steel is one of the most important materials used by humanity, utilised in everything from trains to cutlery. Last year, we produced over 1860 megatonnes of steel in the world, dwarfing the second most used metal in the world, aluminium by a factor of 30. Steel is very useful, but its production also generates nearly 1.9 tonnes of carbon dioxide for every tonne of steel produced and accounts for up to five per cent of total world carbon dioxide emissions.
Clearly, reducing the carbon dioxide emissions of steel would be important in the shift to a low carbon economy and most significant to Australia with our giant iron ore and coal industry.
Why is low-carbon steel important?
The great majority of the world’s steel is produced from ore using the blast furnace route to produce iron and oxygen steelmaking to make steel from the iron. In this two-step process, the carbon (in the form of coke) provides both the energy to fuel the production of iron but also to chemically remove the oxygen from the iron ore to produce iron and carbon dioxide. Carbon plays some role in the steelmaking process, but the great majority of carbon dioxide generated is in this ironmaking stage.
Simply put, if we can replace carbon in the ironmaking stage of the process, we would largely de-carburise (remove the carbon from) the steelmaking process and ‘low-carbon steel’ would not just be a politician’s buzz word.
Can low-carbon steel be achieved?
There is some very good news on this front. Yes, hydrogen can be used to replace carbon. In fact, it has been demonstrated at industrial scale that hydrogen can entirely place carbon as a fuel and reactant to remove oxygen in the ironmaking process. As recently as 2005, a plant operated in Trinidad and Tobago produced several hundred thousand tonnes of iron made from Hydrogen and this was successfully converted into commercial grade steel.
Now the bad news (or at least the complicated part).
Whilst this is technical feasible, there are several serious barriers to this becoming the new way to make steel namely:
- The current dominant technology for making iron, the blast furnace, is not necessarily suitable for the hydrogen production of iron, and so with so much investment in that technology, changing to another technology would be economically difficult for industry.
- The technology that is most easily adapted to hydrogen is direct reduced ironmaking (DRI) of which there are several variants. This technology is not suited to dealing with high gangue ores (unwanted minerals or other material in which valuable minerals are found), that are common around the world, so the introduction of hydrogen DRI production would also be challenging to the iron ore industry and likely to lead extra costs and energy in the subsequent steelmaking step.
- Current ‘green’ routes to making hydrogen (i.e. using renewable energy) are themselves expensive and not currently anywhere near the scale of hydrogen production required by steel plants.
- The so called ‘grey’ route for making hydrogen (i.e. using natural gas as the feedstock) is currently less expensive than green production but also generate significant carbon dioxide. Some industry experts advocate that the grey route is a good intermediate while renewables and electrolysis technology for mass production of hydrogen are developed.
There are significant research programs in the EU, North America and emerging in Australia to address these issues. In my own laboratories at Swinburne, we have active projects looking at these different aspects of the potential hydrogen revolution for metal production. These projects require not only scientific investigation of how hydrogen behaves at high temperature with different ores, but also techno-economic analysis of different options. Any shift to low-carbon steel will require both technical and economic know-how.
In summary, ‘low-carbon steel’ is not a silly buzzword. One of the world’s major industries could be effectively decarburised but there are significant technical and economic hurdles that need to be addressed.
-
Media Enquiries
Related articles
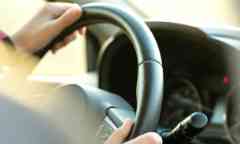
- Social Affairs
- Health
Swinburne leads world-first medical cannabis driving trial
Swinburne researchers are spearheading a world-first trial to evaluate whether patients can drive safely while on prescribed medical cannabis
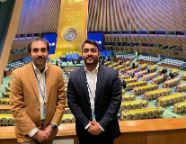
- Technology
- Sustainability
PhD student goes to the 2023 UN Water Conference
School of Engineering PhD student Vishnu Pillai recently landed the prestigious opportunity to attend the 2023 UN Water Conference in New York, thanks to his pioneering work on water sustainability solutions.
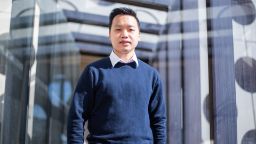
- Technology
- Engineering
Newest Google recruit a Swinburne success story
Swinburne engineer and computer sciences student Chuong Ho has been offered the role of a lifetime as a Google software engineer
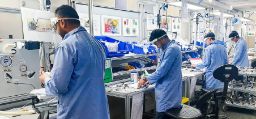
- Technology
- Science
- Engineering
How entrepreneurship saved Aussie lives when COVID-19 hit
Swinburne alum Jefferson Harcourt spearheaded the rapid development of thousands of ventilators early in the COVID-19 pandemic, saving countless lives
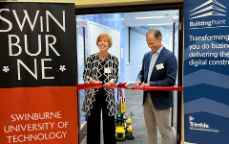
- Technology
- Engineering
Swinburne launches Trimble Technology Lab to create next_gen workforce
The first state-of-the-art Trimble Technology Lab in Australia has opened at Swinburne. It enables learning about new digital technology applications in civil engineering and construction.
-
- Social Affairs
- Health
Swinburne leads world-first medical cannabis driving trial
Swinburne researchers are spearheading a world-first trial to evaluate whether patients can drive safely while on prescribed medical cannabis
Tuesday 28 May 2024 -
- Technology
- Sustainability
PhD student goes to the 2023 UN Water Conference
School of Engineering PhD student Vishnu Pillai recently landed the prestigious opportunity to attend the 2023 UN Water Conference in New York, thanks to his pioneering work on water sustainability solutions.
Friday 05 May 2023 -
- Technology
- Engineering
Newest Google recruit a Swinburne success story
Swinburne engineer and computer sciences student Chuong Ho has been offered the role of a lifetime as a Google software engineer
Monday 07 November 2022 -
- Technology
- Science
- Engineering
How entrepreneurship saved Aussie lives when COVID-19 hit
Swinburne alum Jefferson Harcourt spearheaded the rapid development of thousands of ventilators early in the COVID-19 pandemic, saving countless lives
Friday 04 November 2022 -
- Technology
- Engineering
Swinburne launches Trimble Technology Lab to create next_gen workforce
The first state-of-the-art Trimble Technology Lab in Australia has opened at Swinburne. It enables learning about new digital technology applications in civil engineering and construction.
Wednesday 28 September 2022