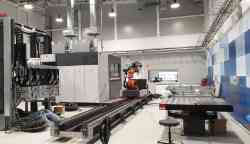
Swinburne-CSIRO National Industry 4.0 Testlab
The world-class Swinburne-CSIRO National Industry 4.0 Testlab provides fully digitally supported engineering and manufacturing solutions for parts, processes and entire systems for automotive, aerospace, production and much more.
The Swinburne-CSIRO National Industry 4.0 Testlab for Composite Additive Manufacturing builds on strong collaboration and joint research with the Australian Manufacturing and Materials Precinct in Clayton.
The centrepiece of the Testlab is the world’s first industrial scale 3D printing multilayer approach to near net composite manufacture. The process has been developed by world-leading Austrian engineering company Fill, to Swinburne’s specifications and in consultation with an industry consortium.
Fill’s unique multilayer printing technology enables us to rapidly produce cost-effective commercial grade fibre-reinforced composite parts with minimal preform trimming at a lower cost, with reduced waste and improved production quality.
The multilayer process has allowed us to build Australia’s first mature Industry 4.0 carbon fibre composite product Testlab where we create opportunities for our industry partners to innovate their products, supply chain, and production or delivery systems, aiming for optimisation in performance, cost and sustainability.
Showcasing the Testlab
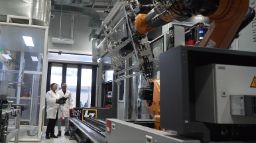

Take a tour
Our equipment
The MULTILAYER is designed to produce near net shape 2D stacks in short cycle time at industrial scale. The machine offers high flexibility in part design and maximum material saving at extremely high speed using up to 16 independently working material unwinding units for tape-laying. The units unwind material directly on the stacking table. The stacking table is designed to be rotatable, so this allows a different orientation of the single layer. Individual layers are bonded using ultrasonic welding, which prevents movement and misalignment of tapes and layer to ensure highest precision of the tape layering.
Our partner Langzauner supplies our press, which is a top of the line curing press for consolidating parts after laying and preforming. The press produces finished parts at highest speeds and quality for a large variety of heated and non-heated tools that can be custom-made for different applications.
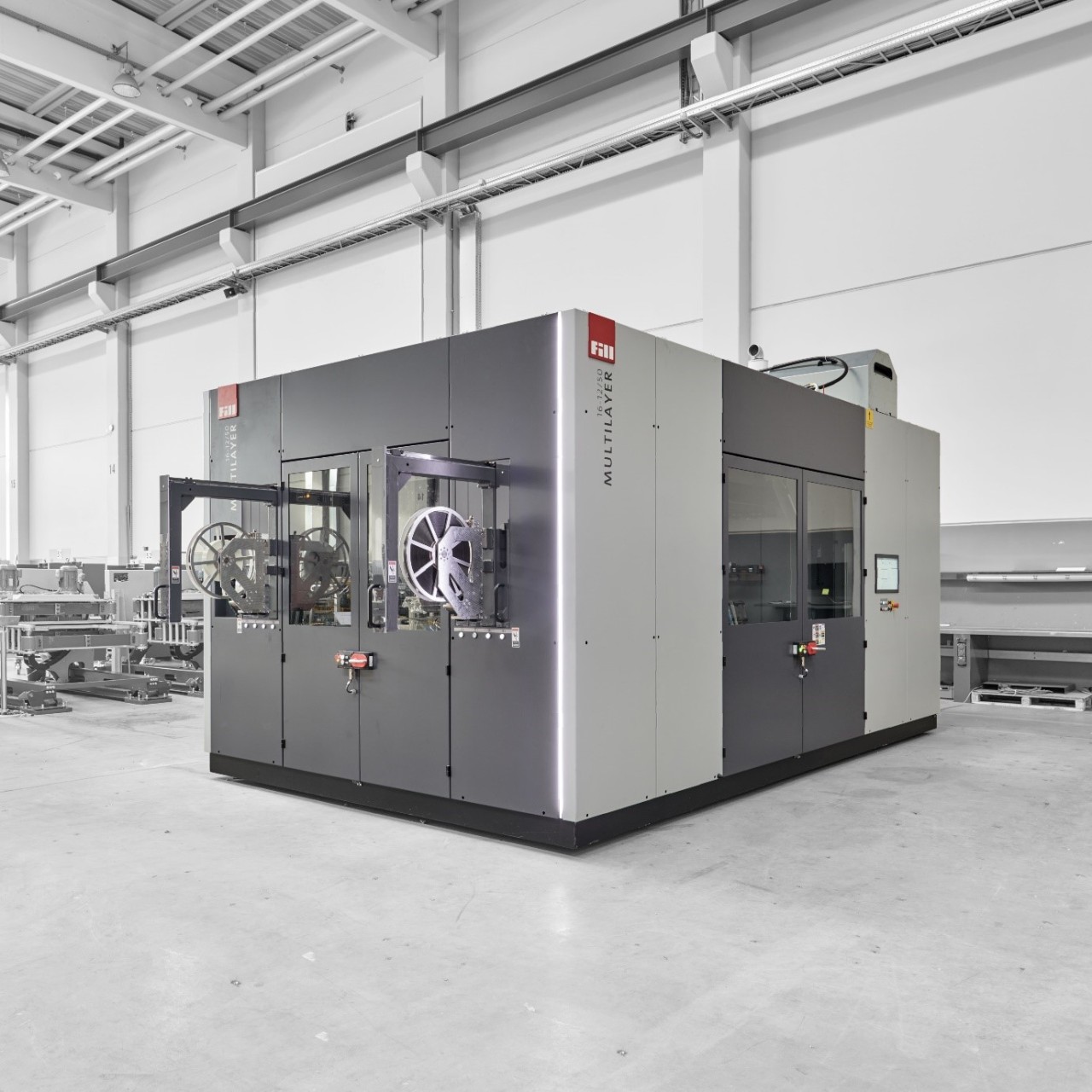
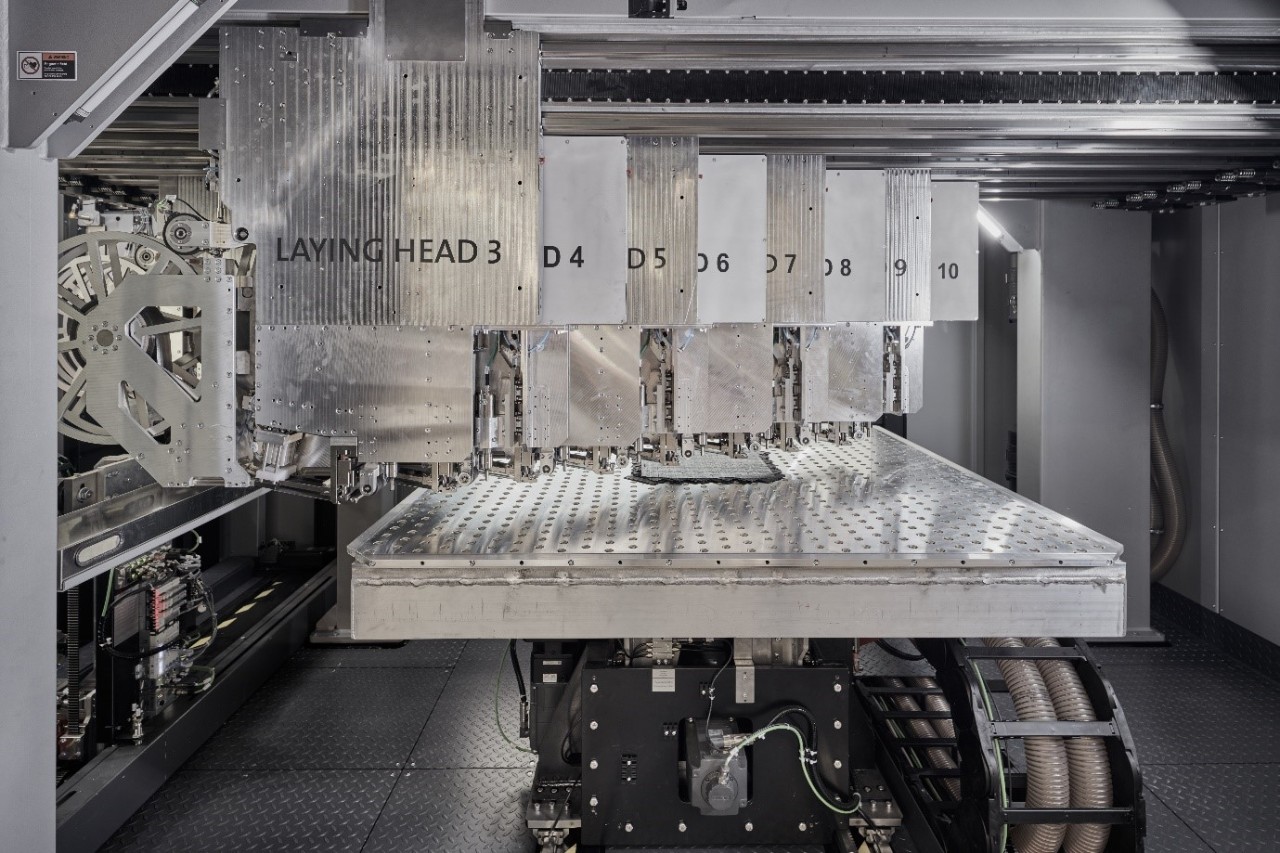
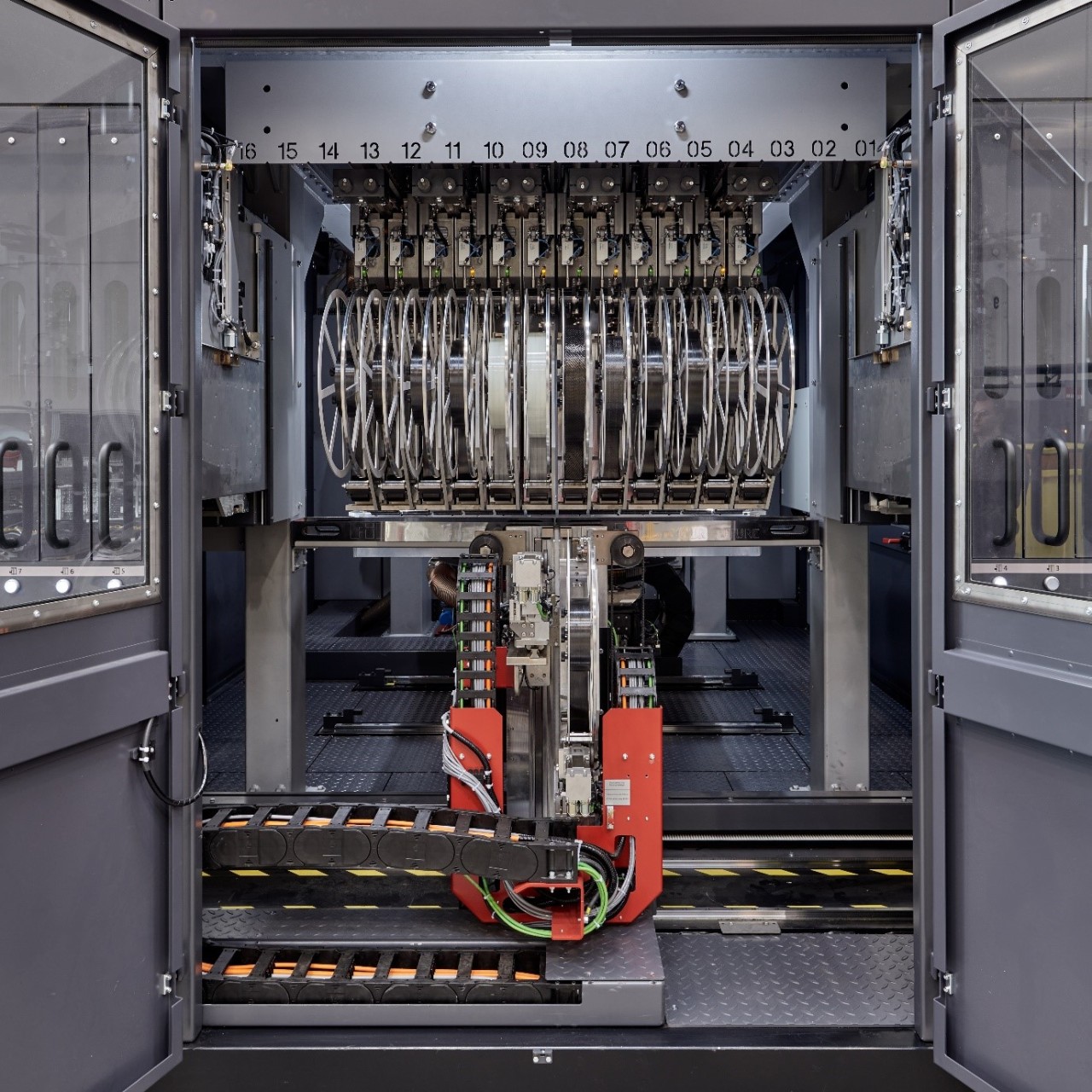
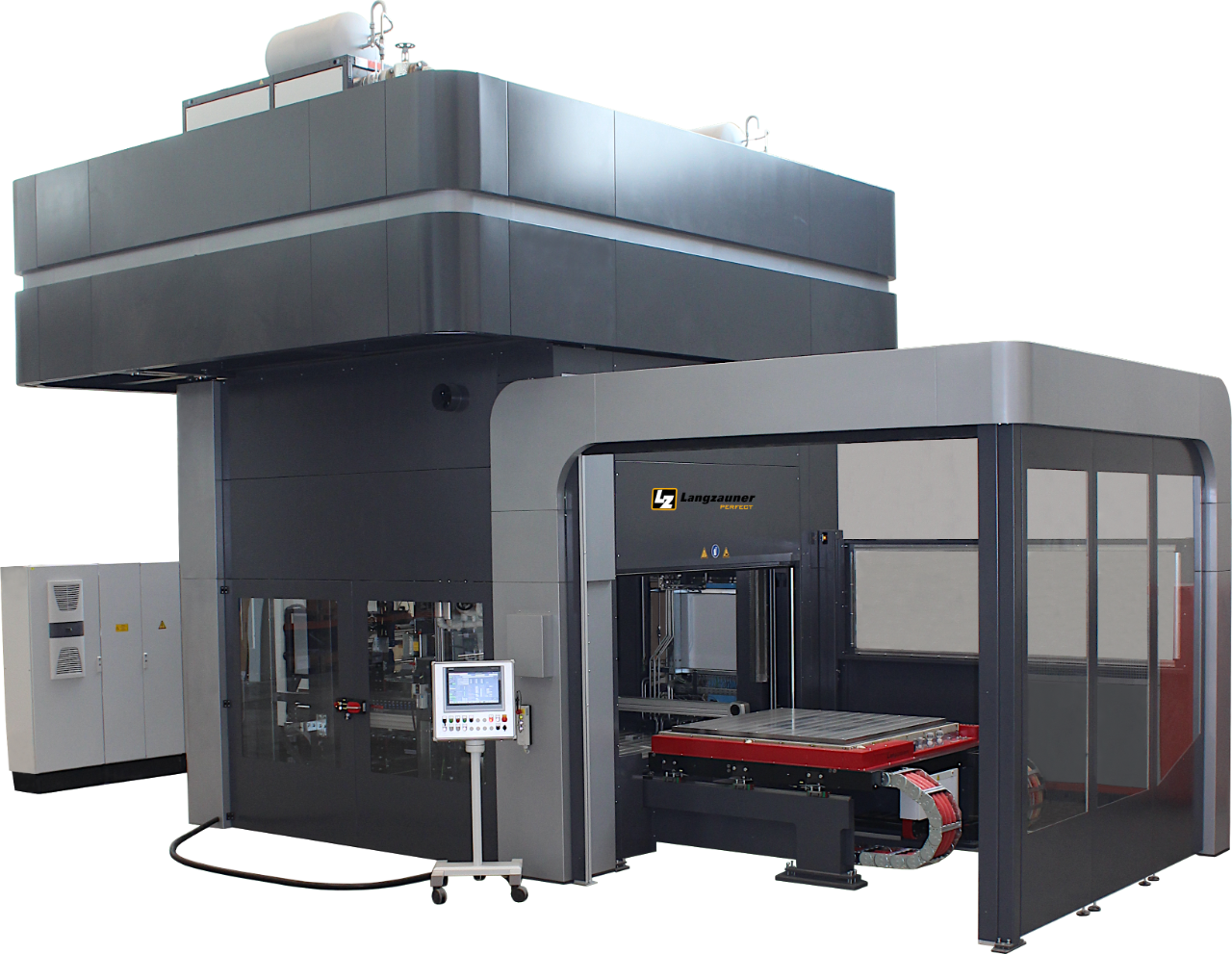
-
Multilayer outside view
-
Multilayer laying table and heads
-
Multilayer tape spools
-
Langzauner Press
Our projects
This project spearheads the digitalisation of engineering and manufacturing processes and advancing capabilities for process and product optimisation through digital twinning and the Internet of Things (IoT).
Through this, we aim to achieve a leap forward in increasing the production rates and quality of composite part manufacture, while significantly lowering the cost of production.
Swinburne has established partnerships with Australian companies and global economies to undertake Industry 4.0 platform capability development. The project leverages the potential of cutting-edge computational design for multi-target optimisation: performance, cost, Takt time, etc.
In this project, we seek to develop XR (extended reality) technologies that will help virtually simulating part design and production before making it physical, but also to do training and upskilling workers to perform associated manual production tasks or quality control for these very parts guided by visual cues ensuring execution to the highest standards. Depending on which parts comes over the assembly line, the exact, relevant instructions are given to the workers what to do with it. This includes providing feedback on the execution of tasks using motion capture to prevent injury.
Project partners: MAGNA Steyr, TU Graz
This project aims to push the boundaries of multi-target computational design optimisation and design/manufacturing planning and automation. We use cutting-edge software tools tying together multiple Computer-Aided Engineering systems to create part designs for structural and functional components in cars, combining materials as hybridised stacks for localised reinforcement within the same composite structure at unprecedented speed in the multilayer. Geometry and processes are optimised for performance and cost at the same time.
Project partner: Ford
This project provided proof of concept evaluations and characterisation of the Multilayer technology for high-speed prototyping of aerospace grade composite components. Different layup configurations were produced using tape feedstock containing a high-end thermoplastic polymer matrix reinforced with aerospace-grade continuous carbon fibre.
Project partner: Boeing USA
Engineers from Quickstep and researchers from the Testlab jointly developed a new production process by combining high-speed tape layup concept, Double Diaphragm Forming and Qure composite curing technology. The joint R&D team developed and tested a one-shot 3D forming and cure process to produce composite components. Developed and industrialised by Quickstep, Qure is a unique and patented out-of-autoclave processing method.
The project was jointly funded by Quickstep and the Australian Federal Government.
Project partners: Quickstep, Innovations Connections
Swinburne collaboration network
We collaborate closely to leverage Swinburne’s product design, strategic design and engineering expertise to create novel solutions for manufacturing to Industry 4.0 standards, product, systems, strategies for sustainability and digitalisation.
This includes Virtual and Augmented Reality for enhanced engineering and product planning and verification, as well as the development of digitally enhanced innovation networks for companies to access global supply chains stretching to Circular Economy applications.
-
Manufacturing Futures Research Platform
-
Factory of the Future
-
Industrial Digital Transformation Hub
Our people
-
Professor Boris Eisenbart
Research Director, Industry 4.0 Testlab; Program Leader, Digital Design -
Jimmy Thomas
Facility Manager, Industry 4.0 Testlab
In the news
-
- Technology
- Engineering
New facility to put Swinburne and CSIRO at forefront of manufacturing digitalisation
The National Industry 4.0 Testlab in Composite Additive Manufacturing is the first of a network of six state-based Industry 4.0 Testlabs established across Australia.
Friday 31 July 2020 -
- Technology
Global Innovation Linkage success for Swinburne and partners
Swinburne awarded $1 million funding towards $3.5 million project focused on Industry 4.0 manufacturing.Friday 12 April 2019
Contact the Industry 4.0 Testlab
If you would like to find out more about the Industry 4.0 Testlab for Composite Additive Manufacturing, or get involved in a project, please contact us at CompositesTestlab@swinburne.edu.au.